A Beginner’s Guide to Torque Motors
Learn everything you need to know about torque motors, including what they are, advantages and applications, and the emergence of precision torque motor technologies.
August 14, 2024
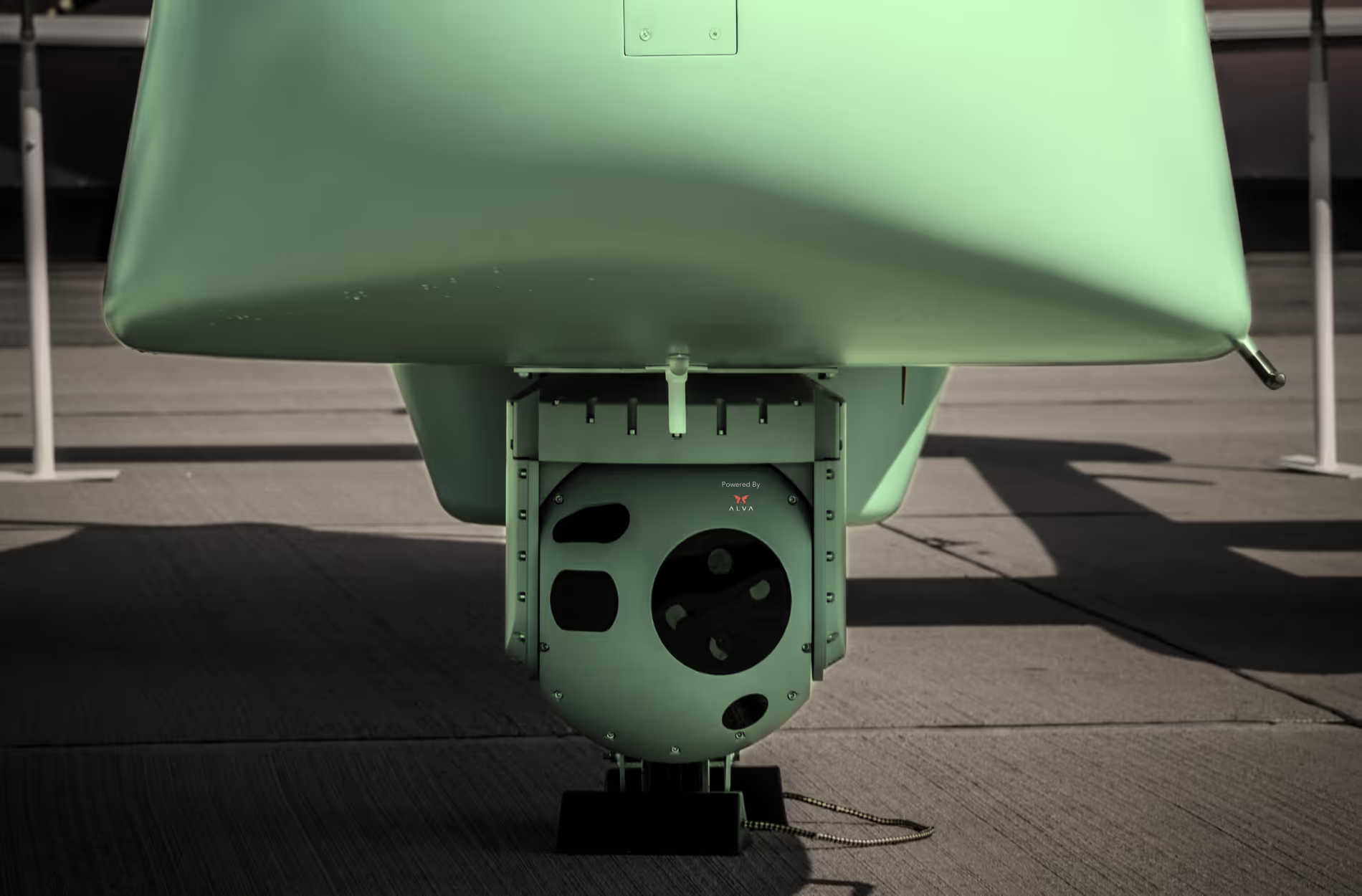
What is a Torque Motor?
A torque motor is a type of brushless, permanent magnet motor. They are often used as a direct drive with the mechanical load attached directly to the motor’s rotor without any intermediate gears, belts or couplings. Typically, torque motors offer high torque at no or low speed.
Torque motors are often supplied in a ‘frameless’ format – in other words, a rotor and stator without any mechanical housing, bearings or couplings. Most torque motors have a low axial height with a large bore compared to outer diameter. The rotor and stator are simply mounted directly to the host equipment’s mechanical parts. Some torque motors offer the rotor inside the stator, others offer the rotor outside the stator.
Unlike traditional motors, selection of a torque motor is based on torque rather than power. Two factors should be considered in the selection of the most suitable motor - peak torque and continuous torque. The nature of the application will determine which is the more important.
What are the advantages of Torque Motors?
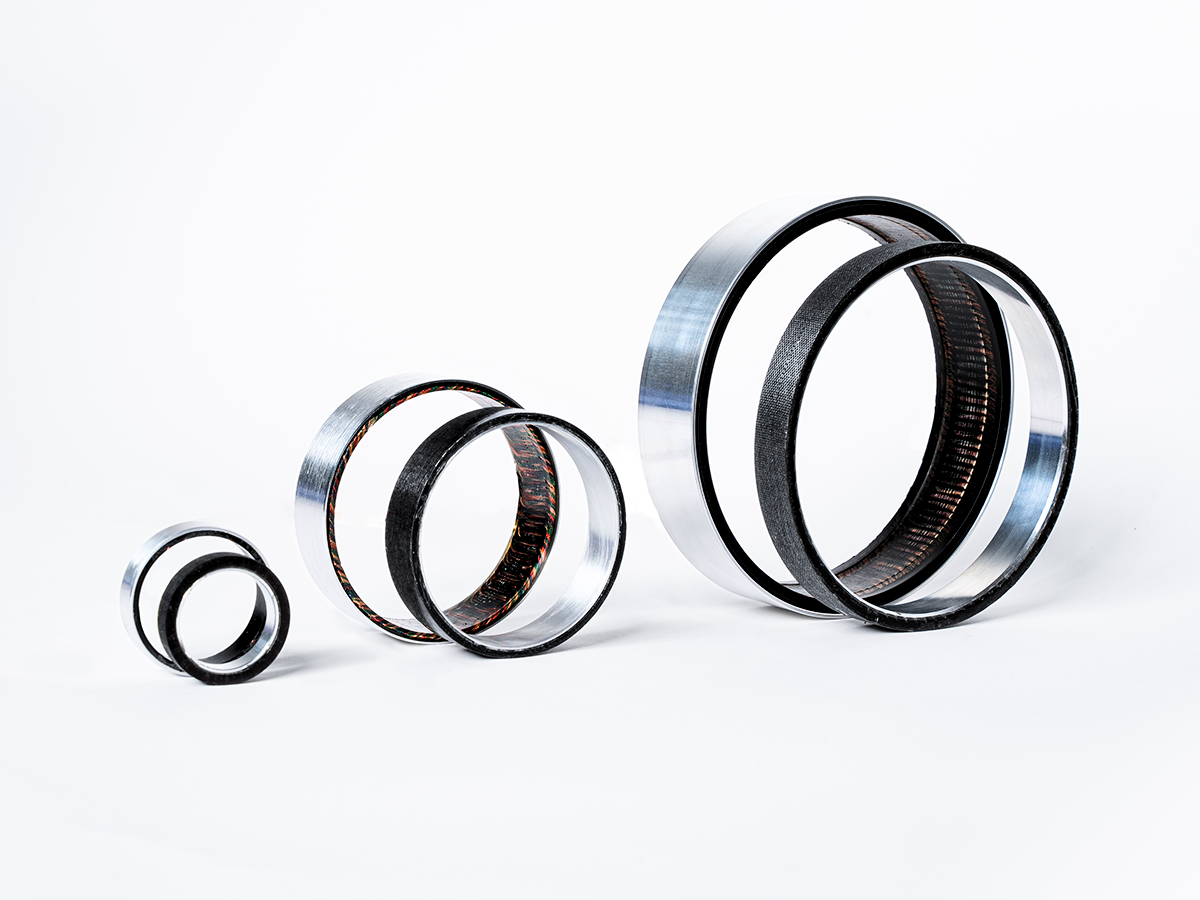
Torque motors offer many advantages over more traditional motors:
Brushless design: No wear and massively reduced service/maintenance costs.
Cost advantage when used as a direct drive: If a torque motor is used as a direct drive, the material and assembly costs of gears, belt drives, or couplings are removed. Such cost advantages are most likely in applications which do not need extremely rapid acceleration of very large mass or inertia.
Compact & lightweight: A large bore relative to the outer diameter and a low axial height makes the mechanical design engineer’s job easier when there are tight size and weight constraints. The torque motor’s basic format permits mechanical, electrical, hydraulic or optical parts – most notably slip rings - to pass through the centre of the motor. Size and weight advantages are maximised when the torque motor is used as a direct drive. Torque motors offer unparalleled torque to weight ratio.
Low cogging: This derives from the large number of magnetic poles and ironless or slotless electrical designs can achieve virtually no cogging due to the symmetric magnetic interaction between the stator and rotor.
High dynamic performance: The inherent torque and mechanical characteristics enable a stiff servo design with low or no hysteresis.
High torque at no/low speed: By increasing the number of pole pairs of the stator and rotor the torque capacity can be sustainably increased.
High Reliability: Especially when used as a direct drive since the number of moving, mechanical parts is minimized and so mean-time-between-failure is maximized.
Reduced vibration and acoustic noise: Removal of intermediate gearing, belt drives, or couplings, and simple mounting to the host structure, will eliminate potential sources of vibration and acoustic noise.
Typical applications of Torque Motors
Torque motors are typically used in a wide range of applications, including:
- Electro-optic equipment
- Exoskeletons
- Humanoid robotics
- Machine tools
- Machine turntables
- Maritime thrusters
- Precision gimbals
- Prosthetics/bionics
- Radar systems
- Reconnaissance pods
- Service Robots
- Remote controlled weapons systems
- Metrology devices
- Rotary joints
- SAT-COM equipment
- Semiconductor equipment
- Surgical robots
- Target designators
- Unmanned vehicles
- Weapon seekers
- Drones
- Industrial robots
What is a Precision Torque Motor?
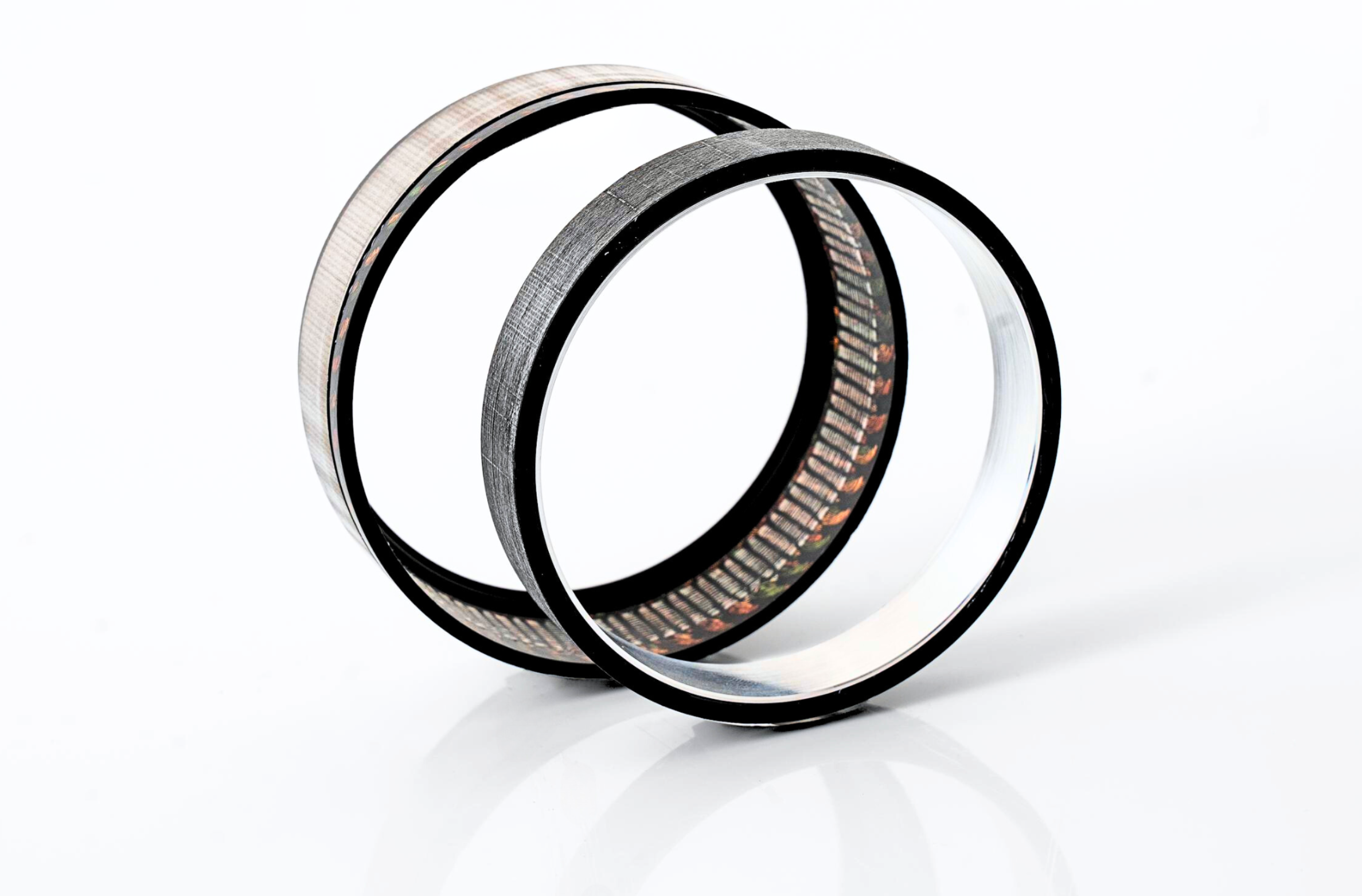
A precision torque motor refers to a torque motor with extremely low cogging; ultra compact format and very high torque relative to its size or weight. Typically, precision torque motors use advanced production techniques, such as Alvas FiberPrinting™ technology, to maximise the packing density of motor windings in the motor’s stator. This enables superior dynamic performance for the motor’s size or weight.
Dr. Nicolas Giraudo
Chief Commercial Officer
+49 40 63 69 8152
Fossegrenda 1,7038 Trondheim, Norway
All rights reserved ©2025