How do Brushless Motors work?
Everything you need to know about brushless motors, including how they work, how they compare to brushed motors, their advantages and applications.
August 23, 2024
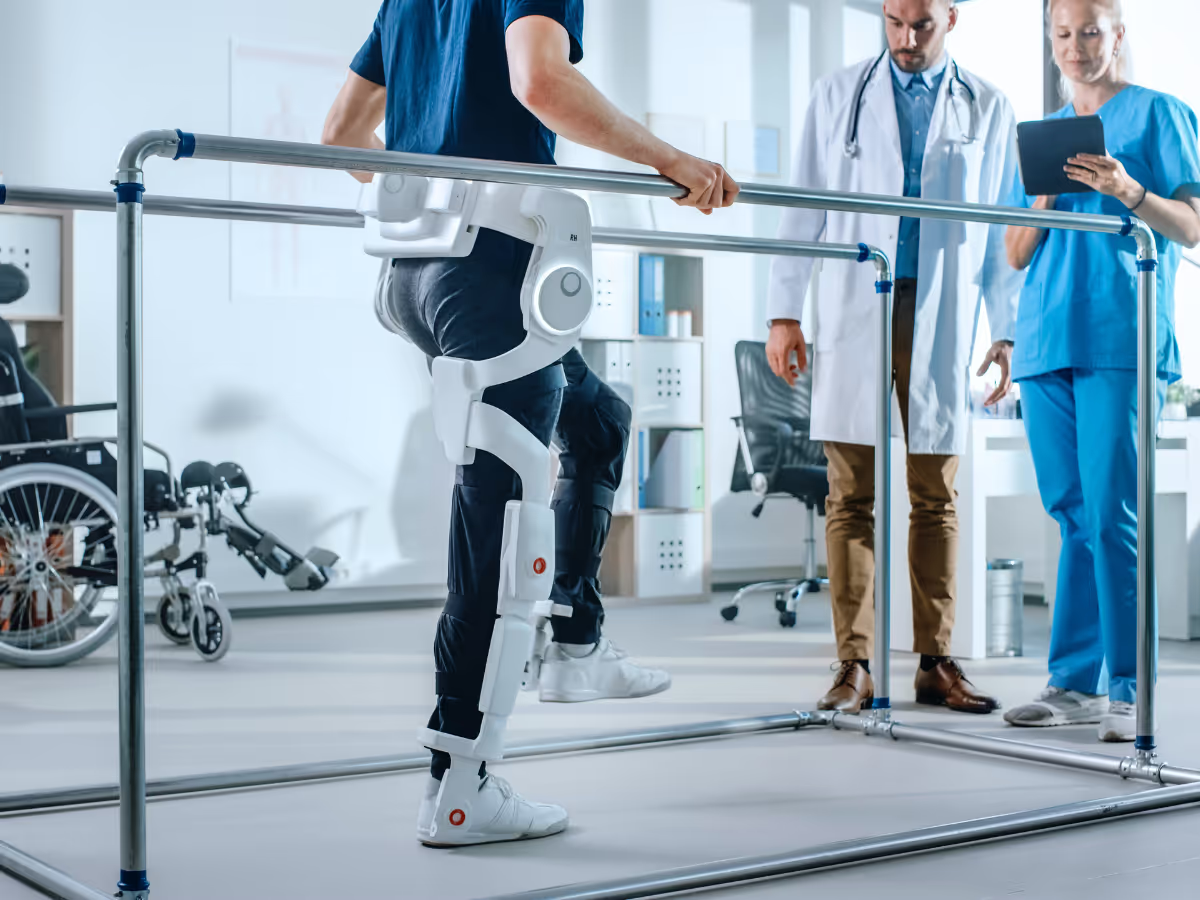
Brushless motors, also known as BLDC (Brushless Direct Current) motors, are synchronous and electronically commutated motors. They are reliable, powerful and efficient motors, used in many applications. Knowing the strengths and weaknesses of brushless motors and what your options are, is key to designing the best drive system for your needs.
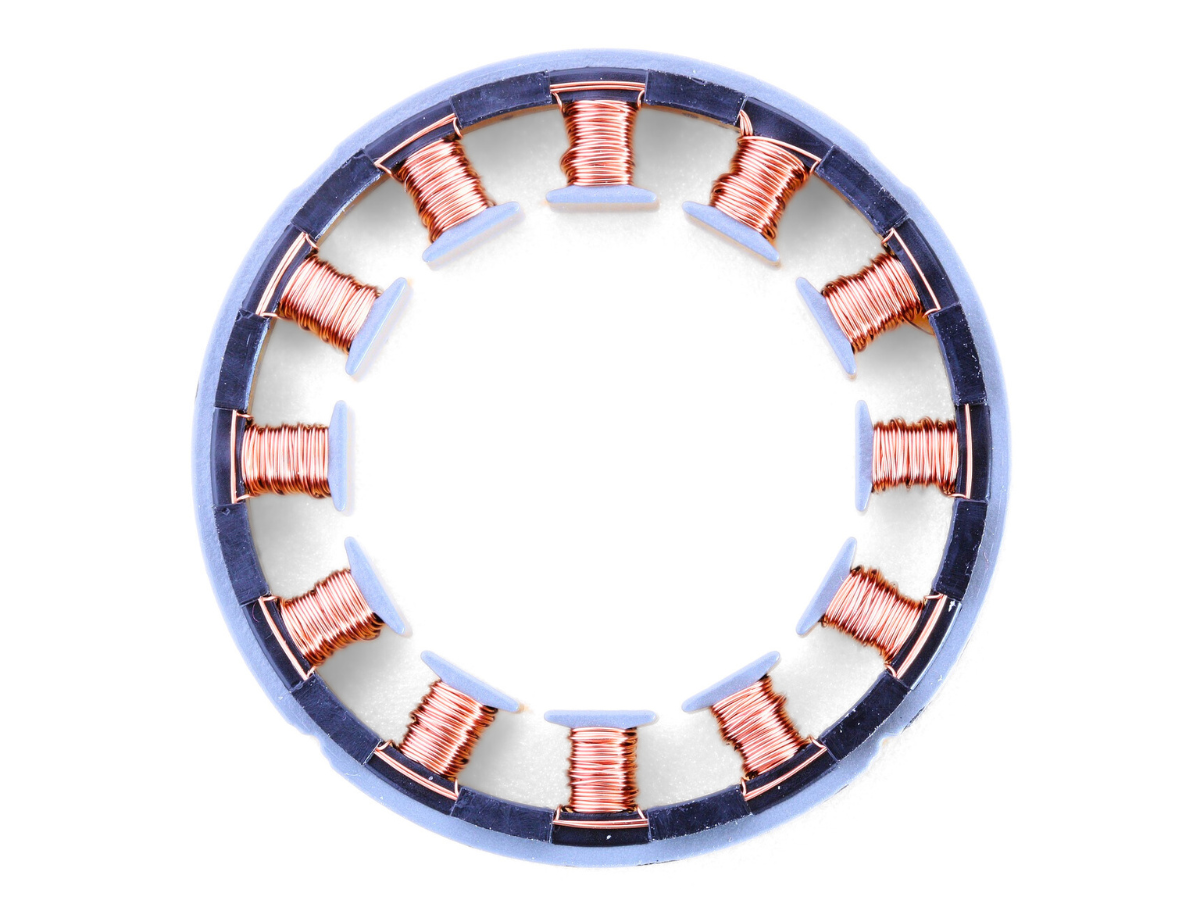
How Does a Brushless Motor Work?
Brushless motors work by creating an alternating electric current in the stator’s copper windings. These interact with the magnets on the rotor, creating motion. When an electric current flows in a copper wire, a magnetic field is created around it. If multiple wires are wound together, or a higher current is applied, an even stronger magnetic field is created. When two magnetic fields interact, they create either an opposing or attractive force, which in turn creates motion. Controlling this alternating current thus allows the user of the motor to specify the torque and speed of the motor. In a synchronous motor, the magnetic field produced by the stator rotates at the same speed as the rotor.
A brushless motor uses an electronic drive to control the current in the copper windings, creating a magnetic field that pulls the magnets on the rotor in the intended direction of motion. The current in the copper windings needs to be controlled very precisely to function properly and maintain high efficiency. A common method to control the current is Pulse Width Modulation (PWM).
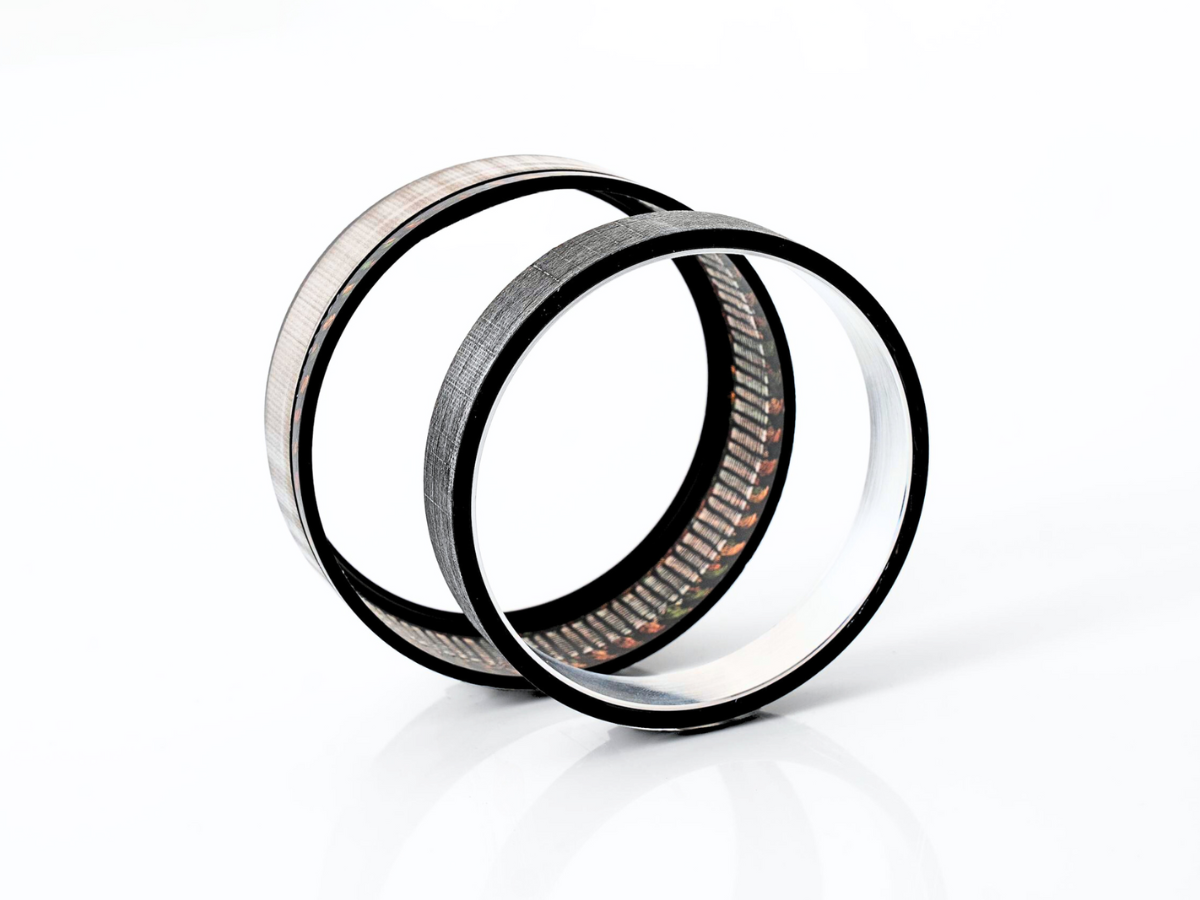
What's the Difference Between Brushed and Brushless Motors?
The primary difference between a brushed and a brushless motor lies in how the motors create an alternating current of the correct frequency. As the motor spins faster and faster, the alternating current needs to change frequency as well.
Brushed Motor
A brushed motor does this mechanically, using brushes to transfer current to the rotor. The copper wires are located on the rotor, and the permanent magnets are located on the stator. When the rotor revolves, the brushes gain and lose their electrical connection to the different phases of the rotor winding, creating an alternating current with the correct frequency.
BLDC Motor
A brushless motor, however, requires power electronics for control. The power electronics have different names depending on the industry, including: electronic speed controller (ESC), servo drive, motor drive, motor inverter, variable speed drive (VSD) or motor controller.
The motor drive controls the amplitude, frequency and phase of the current and voltage applied to the stator’s electric windings. The lack of brushes that mechanically interact with the rotor results in higher reliability and longer life. Control by a motor driver also results in precise control of torque and speed, and improved or more tightly controlled motion.
Strengths and Weaknesses of Brushless Motors (BLDC)
Strengths:
- High Efficiency: Brushless motors convert more electrical energy into mechanical energy, minimizing energy losses.
- Long Lifespan: The absence of brushes and robust construction significantly extends the lifetime of the motor.
- Low Maintenance: Ideal for long-term use, brushless motors require minimal upkeep.
- Precision Control: Electronic commutation enables precise control over speed and torque.
- Quiet Operation: Without friction-creating brushes, these motors run more quietly than brushed counterparts.
Weaknesses:
- Cost: The increased complexity and need for an electronic controller increase the initial material cost compared to brushed motors, but this is compensated for by reduced service or maintenance costs.
- Complexity: The required electronic controller adds to system complexity.
- Initial Setup: Compared to brushed motors, setting up a brushless system demands more time and expertise.
Main Applications for Brushless Motors
Due to the high efficiency, reliability and precision control, brushless motors are the go-to technology in a wide range of industries. They are more widely used than brushed motors in many industries. Some of the main applications for brushless motors, sorted by industry, are:
- Medical Industry
- In industries valuing reliability and precision, BLDC motors are used to power surgical tools, imaging devices, ventilators, and pumps.
- Aerospace
- BLDC motors are used in aerospace to power actuators for wind flaps and wheels, imaging systems and fans.
- Industrial Automation
- Robotic arms, CNC machines, positioning devices, pumps and fans use BLDC motors.
- Defence
- Performance, reliability and precise control are key in many defence applications, from marine and aerial propulsion, to aerial, ground based and marine gimbals.
Brushless Precision Torque Motors
A brushless precision torque motor is a specialized BLDC motor designed for applications that require high torque output and precise control of the motor. Typical applications for precision torque motors include robotics, medical devices, SatCom, metrology, semiconductor manufacturing, and high-precision gimbals.
Brushless precision torque motors allow the design of a system to deliver high and consistent torque at precisely the speed needed, without compromising efficiency or requiring a large motor.
In summary, brushless (BLDC) motors use a motor drive to alternate the motor’s electric current and drive the rotor. BLDC motors are more reliable, efficient and precise than brushed motors, and are in use in a wide range of industries and applications. Brushless precision torque motors are a type of BLDC motor with increased torque output and precision, making it the desired choice for demanding precision applications.
Nicolas Giraudo
Chief Commercial Officer
Fossegrenda 1, 7038 Trondheim, Norway
All rights reserved ©2025