Enhancing the Performance of Rim Drive Thrusters by Employing FiberPrinted™ Motor Technology
Enhance rim-drive thrusters with Alva's FiberPrinted™ motors for superior efficiency and reliability in marine propulsion systems.
August 21, 2024
.avif)
Rim drive thrusters, also known as rim-driven thrusters, offer several advantages that make them a compelling choice in marine applications, from small boats and underwater vehicles to yachts and large vessels. Rim drive thrusters are valued for their efficiency, low noise, compactness, reliability, reduced maintenance, flexibility of placement on the vessel, enhanced maneuverability and environmental benefits.
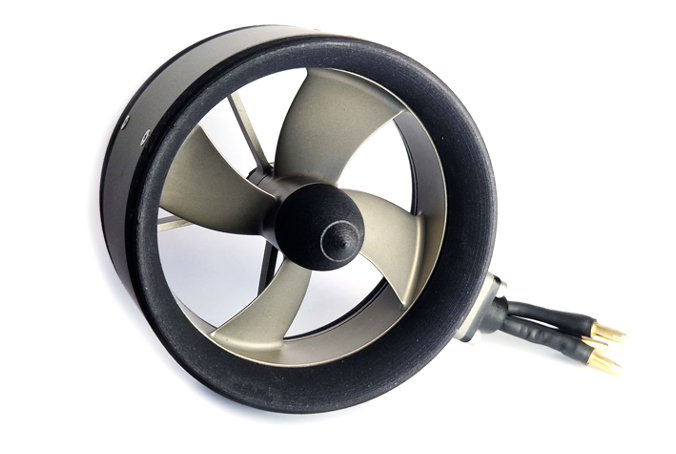
Alva has developed the Hydra-100 rim drive thruster (Fig. 1) demonstrating that the use of FiberPrinting™ technology makes this thruster type even more attractive for many marine propulsion applications. The Hydra-100 thruster consists of a FiberPrinted™ stator integrated into the rim (Fig. 2,a), in combination with a Halbach magnetic rotor integrated with the thruster impeller (Fig. 2,b). The thruster demonstrates superior performances compared to other marine thrusters on the market in the same size category, in terms of higher maximum thrust, higher thrust efficiency and thrust density.
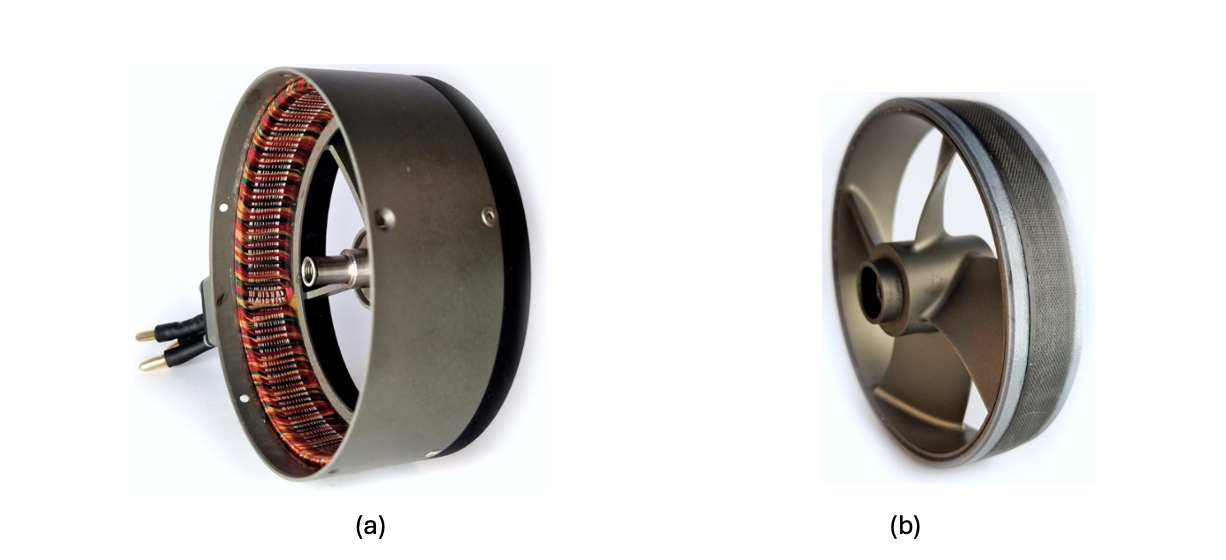
FiberPrinting™ technology enabling superior cooling
The optimal cooling of the FiberPrinted™ stator is possible due to three attributes; thin stator cross-section, thin thermal interfaces within the stator assembly, and the stator being in direct contact with the cooling medium:
1. The cooling ability of a mechanical assembly is dependent on the thermal conductivity of the material and the layer thickness of each material. The main components of a FiberPrinted™ stator is manufactured from highly thermally conductive materials i.e. copper (litz wire strands), steel (lamination ring) and aluminium (thruster rim). In Hydra-100 the thermal interfaces between the main components have been optimised to maximise the thermal performance. For example, the litz wire is tightly packed to ensure good thermal connection between individual copper strands and the steel laminations are coated with a thin thermal epoxy, just thick enough for sufficient electrical insulation.
2. Since a FiberPrinted™ stator is moulded in highly thermally conductive epoxy it is inherently compatible with corrosive liquids and can be fully submerged in both fresh water and salt water. The thruster can therefore be designed with the intent to flush the stator in the liquid the thruster is operating in. Flushing the thin stator in a cooling medium, with the same temperature as the ambient environment, is the most effective cooling method that can be applied without complex solutions.
3. FiberPrinter produces slotless stators which do not have any iron teeth typical for conventional motors, thus the FiberPrinted stators are very thin which significantly shortens the heat removal paths.
The form factor enabling the optimal thruster design
One of the drawbacks of iron-cored motors is the radially thick area occupied by the copper windings wound around the iron teeth. The thin cross-section of a FiberPrinted stator enables design of streamlined thrusters with thin rims (Fig. 3). This will have a significant positive impact on the overall efficiency of the propulsion system due to reduced drag.
FiberPrinting™ enables simple manufacturing of windings with large diameter. The advantages of larger diameter motors in a rim driven marine thrusters are threefold; large impeller, increased cooling surface and increased magnetic lever arm:
1. A large diameter motor allows for larger impellers which have higher efficiency and higher maximum thrust output. A FiberPrinted motor can be produced in any size so the impeller size can be selected based on desired thrust output and never limited by motor size limitations.
2. The cooling surface of the stator effectively increases linearly with the diameter of the stator. A large diameter motor can therefore be cooled more effectively, which allows for higher power-levels without overheating the stator.
3. The torque output of an electric motor is dependent on two factors; the tangential force generated between the stator and rotor, and the distance between the tangential force and the center of the motor i.e., the magnetic lever arm. Therefore, the torque output will increase linearly with the motor diameter if the tangential force remains the same.
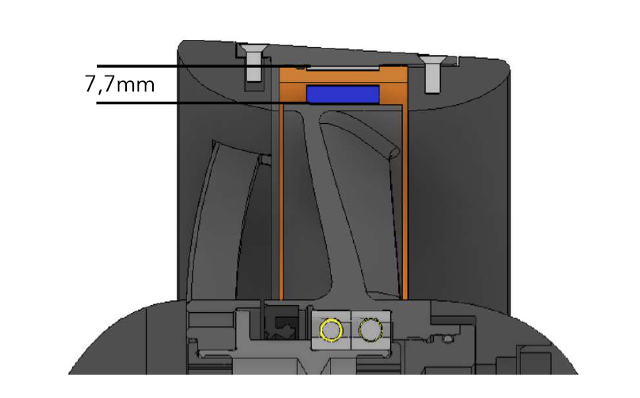
The opportunity to build a more silent thruster
An iron-cored motor optimized for power and efficiency often has relatively high torque ripple due to the asymmetric interaction between the magnetic rotor and the iron teeth of the stator. Torque ripple causes vibrations and audible noise. A FiberPrinted motor has virtually zero torque ripple because the laminations around a FiberPrinted™ winding are perfectly round. Low torque ripple makes the motor silent, allowing for an extremely silent thruster if a FiberPrinted motor is combined with the correct type of impeller.
The intrinsic water protection enabling reliable thruster designs
The active material of Alva’s electric motors, i.e., stator and rotor, are manufactured in such a way that they are inherently suitable for corrosive environments without additional protection required. As mentioned above, FiberPrinted™ stator consists of a combination of litz wire and thermal epoxy. The litz wire has a polymer insulation layer which ensures electrical insulation and protects the copper from corrosion. The litz wire is also potted in thermal epoxy to increase thermal conductivity through the stator and to provide further corrosion protection for the copper strands. The result is a stator that can withstand highly corrosive environments for prolonged periods of time without any degradation.
The laminated core of an iron-cored motor is a difficult component to protect against corrosion due to its complex geometry. The simplicity of the lamination ring within a FiberPrinted™ stator assembly makes it an easy component to protect. The lamination ring is sandwiched in between the stator and a housing, and it’s potted along with the stator which gives it a protection layer on all surfaces.
The rotor consists of magnets with an epoxy layer on all surfaces which are attached to each other and a mechanical rotor through a potting process giving them additional corrosion protection.
Enabling the possibility of thrust boost operation
A traditional iron-cored motor’s power output is limited by the heat development, but also by saturation of the iron teeth. An iron-cored motor is therefore a trade-off between efficiency and saturation margin, since minimizing the teeth section will have a positive impact on the efficiency but a negative impact on the saturation margin.
This trade-off is not the issue in FiberPrinted stators since the magnetic field within the stator lamination is not as strong. It’s weaker since both the stator windings and magnets, and therefore also the magnetic field is distributed further away from the laminations. The magnetic field in the laminations is low enough too virtually never cause saturation even at exaggerated levels of input current. This means that the current-torque relationship for a FiberPrinted motor is linear up to much higher currents than for iron-cored motors, enabling significantly higher torque and power output.
The absence of a saturation limit in combination with the excellent cooling of FiberPrinter motors results in a compact thruster with extraordinary high power-output.
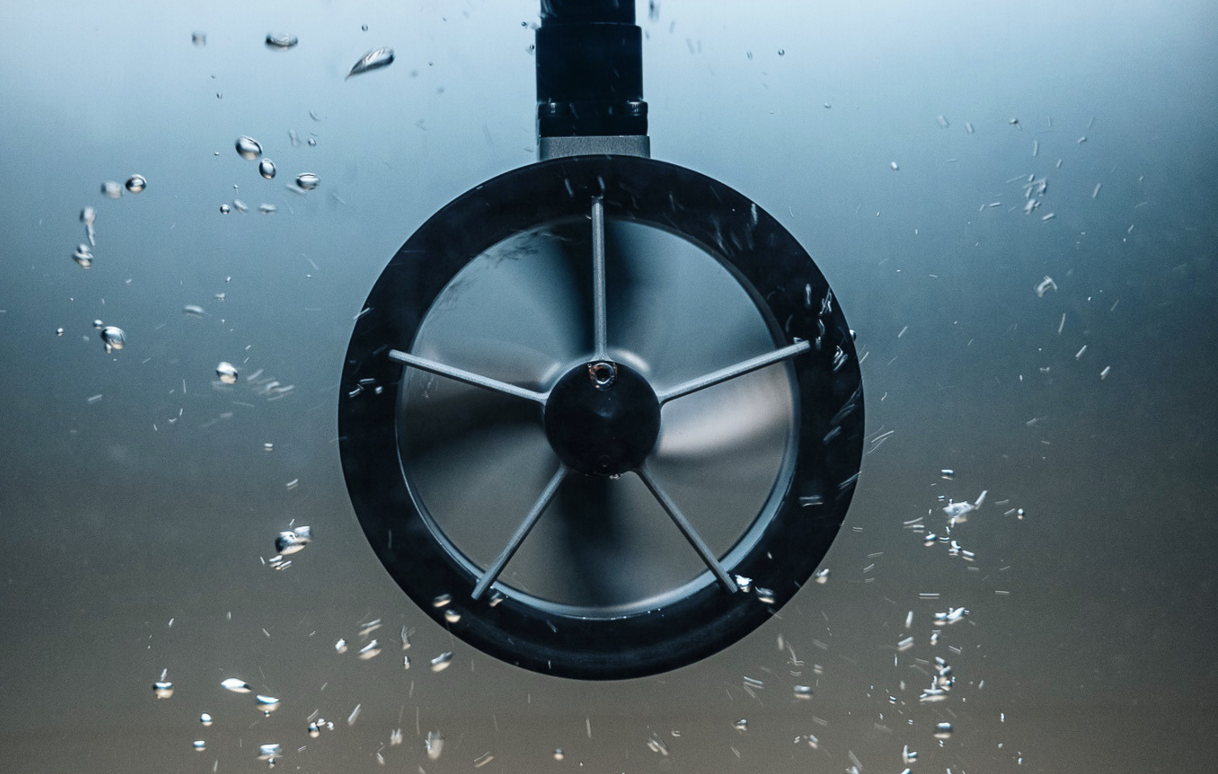
The unique performances and scalability
To summarize the above, Alva’s thruster provides higher maximum thrust and higher thrust efficiency than any other marine thruster on the market in the same size category due to the four inherent properties of FiberPrinted motors: optimal cooling, absence of saturation, zero-cogging, optimal form factor.
The simplicity of Alva’s electric motors, i.e., perfectly cylindrical stator and rotor with only a few design parameters, in combination with low iron-losses, result in an electric motor technology that can be scaled to any size.
Performance data of Hydra-100 thruster based on testing in open water (Fig.4) are presented in Table 1. Dimensions of the thruster can be found in Fig. 5.
Benchmarking versus competitors shows that Alva’s FiberPrinted™ motors enable market leading performance of in terms of continuous thrust density, both gravimetric (Fig.6,a) and volumetric (Fig. 6,b).
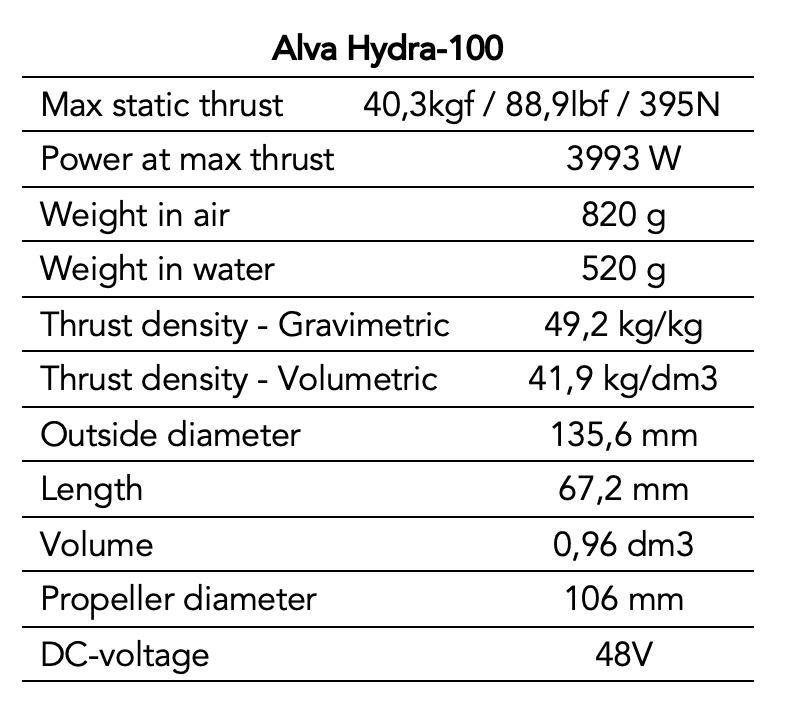
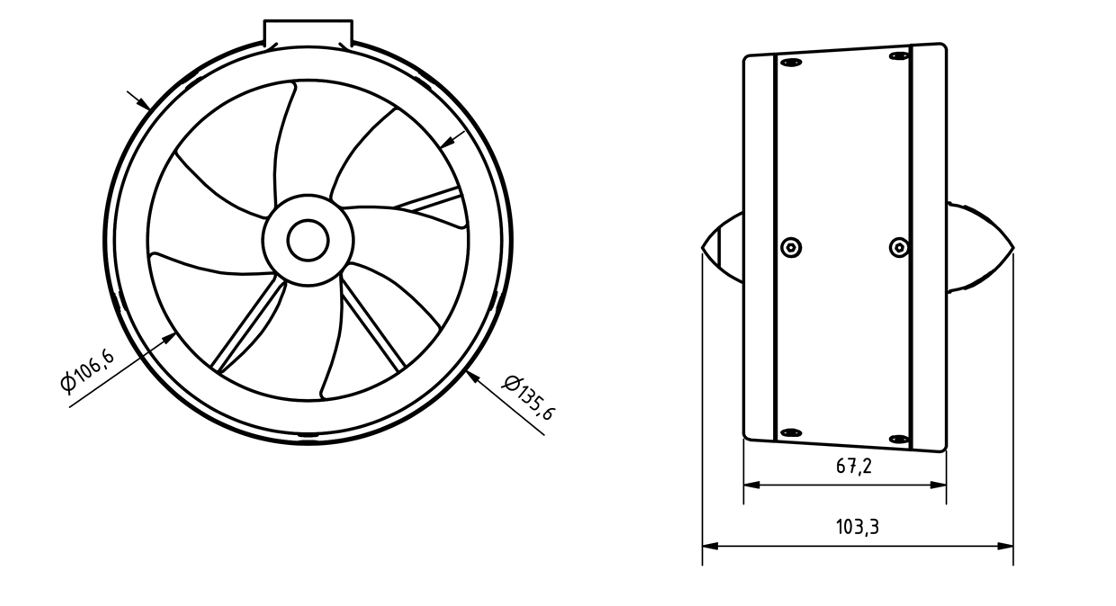
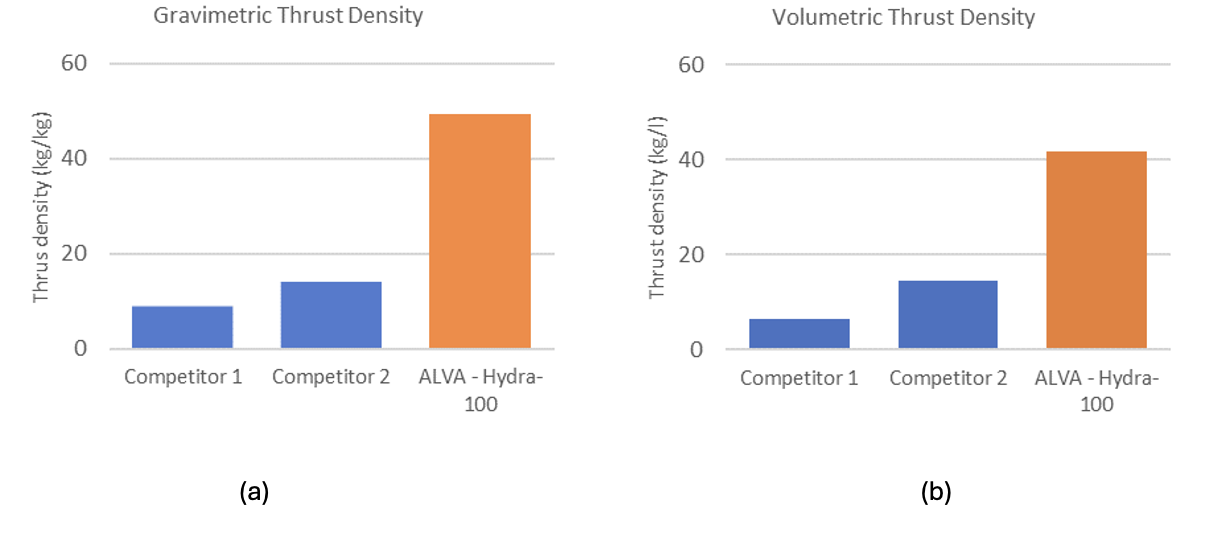
All rights reserved ©2025